Assembly Line by Henry Ford: Model T Production and the Moving Assembly Line
Henry Ford, inspired by Chicago's meat-packing plants, revolutionized automobile production by inventing the moving assembly line, significantly reducing Model T assembly time and democratizing vehicle ownership.
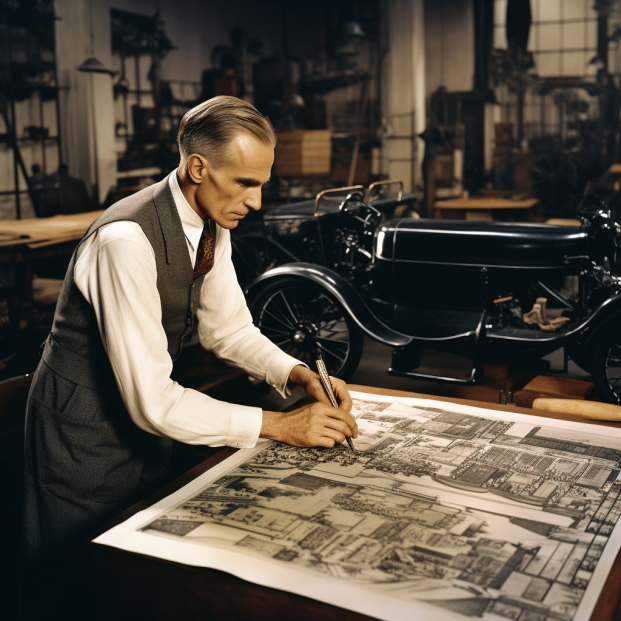
What is the connection between an abattoir and the Model T?
Now, Henry Ford was a genius.
Not only were his ideas and innovations far ahead of his time but his self-marketing and promotion were too.
The story goes that Henry Ford took inspiration from a Chicago meat packing plant in the early 20th Century. He saw something – be it in person or a photograph - that inspired him to revolutionize production at the Ford Motor Company factory.
Ford's innovative practices not only revolutionized automobile manufacturing but also had a profound impact on other industries, leading to widespread changes in business and manufacturing practices.
How Henry Ford Invented the Moving Assembly Line
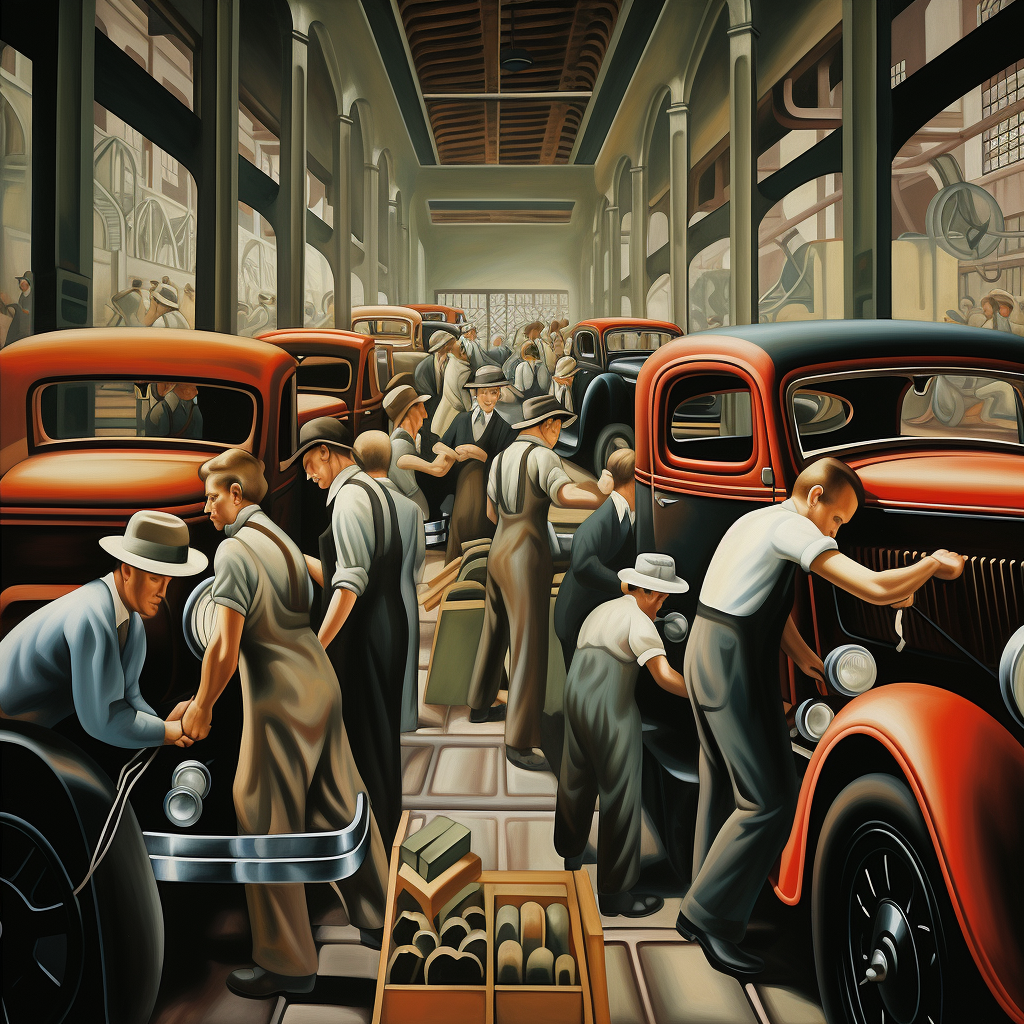
If you are of a sensitive disposition – don’t read.
A meat packing plant in the early 20th Century is a bit of a misnomer. Animals went in, they were slaughtered, disassembled, and packed for onward sale. It was not a particularly sanitary or safe place to be.
There was no aircon, little running water, and god knows in summer you didn’t want to be around a dead and decaying hog for too long! Fact!
But, these plants processed an essential part of the food chain (animals) and did it in a way that was quick, effective, and most of all efficient.
These guys did not want to linger so they devised a system.
Instead of all working on one animal at a time, they learned to do one part of the process really well and did it multiple times in quick succession.
In short, they moved the animal carcass around, not the humans.
They hung um, they split um, they disemboweled um and then they hacked off the edible bits in a systematic way before the cuts were cleaned, labeled, and packaged.
Each man did one of these jobs, they were highly skilled in it. Once the job was done, the carcass moved to the next guy and then the next…until all the jobs were done.
At the end of the process, there was no animal. There were cuts of meat for sale.
Henry Ford observed the “disassembly line” of Chicago’s meat-packing plants and, with the help of Ford engineers, was inspired to reverse the process in his factories. The assembly line concept came from watching assembly line work in a completely different industry.
He realized that the method they were currently using at the Ford Motor Company – where automobiles were assembled by groups of workers who worked together to build each car from start to finish – was costly and time-consuming.
If he wanted to realize his dream of bringing the automobile to the masses, something would need to change.
The moving assembly line was born. Instead of the car staying in place, the assembly line worker stayed in one place. They got highly specialized in their one thing – be it wheels or gears or wing mirrors. That was their patch, and the car could only move on once they had done their bit.
What were the key outcomes for the Ford Motor Company?
A drastic reduction in assembly time for a Model T chassis from 12.5 hours to approximately 1.5 hours at Ford’s Highland Park Plant. As the moving assembly line was implemented, workers began to specialize in specific tasks, which significantly increased production efficiency.
The increase in car production from the assembly line Henry Ford introduced meant that the price of Model T cars dropped significantly.
This lead to a democratization of vehicle ownership due to mass production and reduced costs. The assembly line workers themselves could own Model Ts.
An altered employment landscape, with increased demand for specialized, yet often monotonous, labor.
What can you take from the Henry Ford Assembly Line story?
1. The Power of Innovative Thinking:
- Ford desired to create an automobile that was financially accessible to a broad population, moving beyond the luxury market.
- Never underestimate the impact of a fresh perspective and innovative thinking in overcoming seemingly insurmountable challenges. Swift & Co and their disassembly line could not have dreamed that their approach would be taken onboard by one of the biggest industrialists of all time and the Ford Motor Company.
- Your vision, however ambitious, can be achieved with inventive solutions and a willingness to diverge from established norms. The first Ford assembly line has been reproduced in the Henry Ford Museum.
2. Democratization Through Scalability:
The advent of the moving assembly line enabled mass production, which meant the price dropped allowing a much wider demographic to afford vehicles.
Take a leaf out of the Ford Motor Company book - while moving assembly lines might not be what you need to get the edge. it certainly could be a lesson in how to scale.
Consider how your product or service can be altered or scaled to reach wider audiences. Your initial offering might cater to a niche market, but innovative production and distribution strategies can broaden your reach and impact.
3. Worker Specialization: A Double-Edged Sword:
- On the Ford assembly line for the Model T, Workers became highly specialized in particular tasks, enhancing efficiency but potentially reducing job satisfaction. So it was that someone could fit a steering wheel or gas tanks for their entire career.
- Balancing efficiency with worker satisfaction is crucial. Consider the human element in your process enhancements and seek ways to maintain or improve employee engagement and well-being alongside productivity.
4. Market Expansion Through Price Accessibility:
- The reduction in manufacturing costs allowed Ford to lower the price of the Model T, expanding its market significantly.
- Pricing strategy is pivotal. Understand how production efficiencies can be translated into pricing strategies that enable market expansion, ensuring your products or services are accessible to diverse consumer bases.
5. The Ripple Effect of Innovation
The introduction of the assembly line didn’t just alter the automotive industry; it reshaped society, impacting living, working, and migration patterns. During World War II, Ford's assembly lines were adapted to produce aircraft engines, further demonstrating the broad applicability of his innovations.
Always seek to understand the broader impacts of your innovations. How will changes within your organization reverberate throughout your industry, society, and beyond?
6. Navigate the Ethical Implications:
- The assembly line presented issues, including labor disputes and concerns over worker conditions and satisfaction.
- Ethical leadership demands a comprehensive view. Be aware of and navigate the potential ethical and social ramifications of innovations, ensuring your progress does not come at an undue cost to stakeholders.
6. Never underestimate the power of a good story
- Did Ford actually go to a meat packing plant? Was the idea actually his? To a large extent, it doesn't matter, for the rest of the time the Assembly Line will be Ford's invention.
Concluding Thoughts
Ford's moving assembly line is emblematic of innovation, offering a rich tapestry from which leaders can draw insights about innovation, scalability, and the broader societal impacts of industrial decisions. Your leadership journey, like Ford's, is intrinsically linked to how you navigate innovation, scalability, and ethical considerations, shaping not just your enterprise, but potentially, the world at large.
Your Reflection
How does innovation shape your leadership and organizational strategy?
How can you balance efficiency, scalability, and ethical considerations within your leadership approach?
Engage with these questions, and you pave the way toward leadership that not only directs but transforms and ethically innovates within your sphere of influence.
Want to know more about Henry Ford's Leadership?
STORIES
All our leadership stories about Henry Ford are available here
BOOKS
Drive!: Henry Ford, George Selden, and the Race to Invent the Auto Age