Jack Welch and Six Sigma
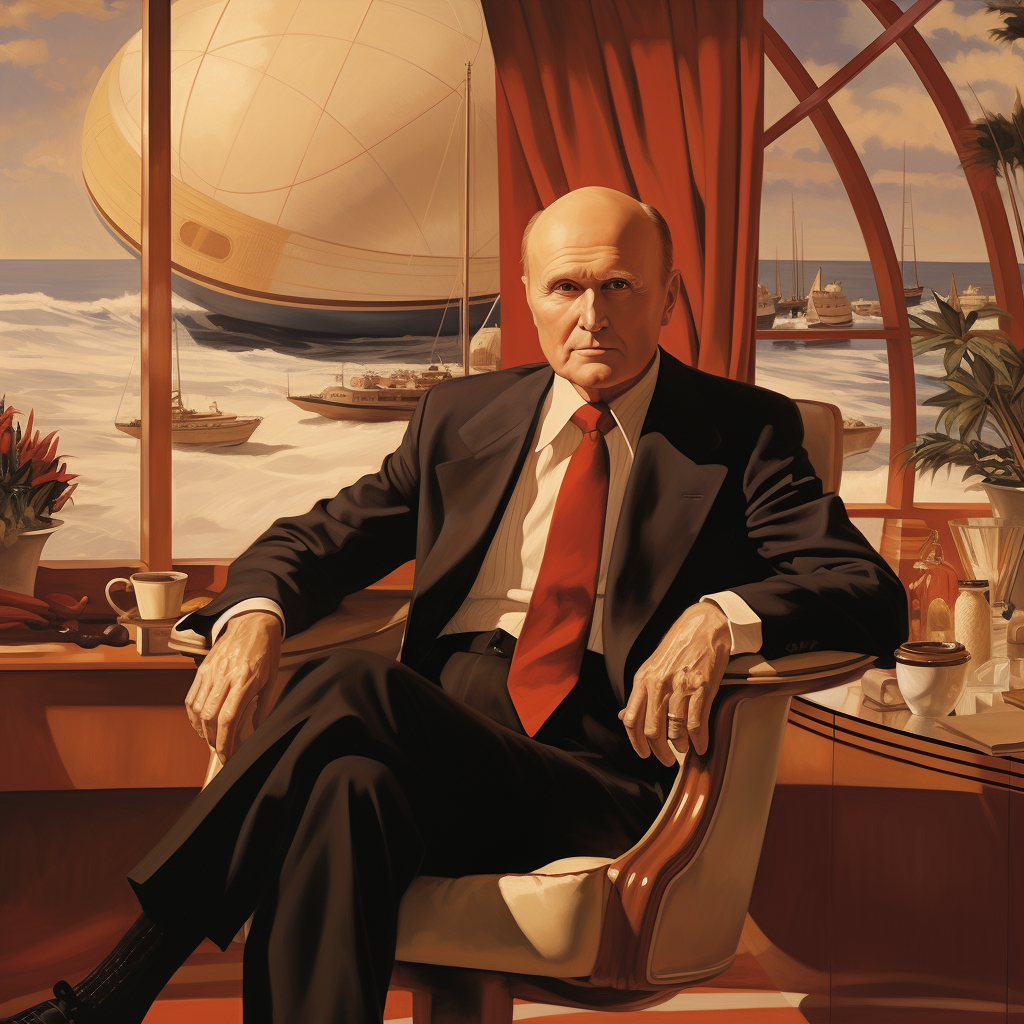
Introduction
In the late 1990s, Jack Welch, then CEO of General Electric (GE), initiated a transformative quality control program known as Six Sigma. This strategic move was not just an adoption of a new process; it was a cultural shift within GE, embedding a commitment to quality and continuous improvement at the heart of the company’s operations.
Welch’s championing of the Six Sigma initiative provides valuable insights into how consistent focus on quality can drive organizational excellence and efficiency.
Factual Details of GE's Six Sigma Initiative
Era: Late 1990s
Location: United States
Event: Implementation of Six Sigma at General Electric
Under Jack Welch's leadership, GE adopted the Six Sigma quality program, a set of techniques and tools for process improvement, originally developed by Motorola. Welch recognized the potential of Six Sigma to significantly enhance GE’s operational efficiency and customer satisfaction.
He aggressively pushed for its implementation across all aspects of the company, tying its principles to performance reviews and business outcomes. The initiative aimed at reducing defects and improving quality in all processes, products, and services.
Key Outcomes:
- Significant improvements in product quality and operational efficiency across GE.
- Estimated savings of billions of dollars due to the reduction of defects and inefficiencies.
- Establishment of a culture of continuous improvement and quality consciousness among GE employees.
Leadership Lessons from Welch’s Six Sigma Initiative
1. Prioritizing Quality in Business Operations:
- Welch’s emphasis on Six Sigma demonstrated how prioritizing quality can lead to substantial improvements in efficiency and customer satisfaction.
2. Embedding Continuous Improvement in Corporate Culture:
- By integrating Six Sigma into GE’s culture, Welch showcased the importance of making continuous improvement an organizational norm.
3. Linking Quality to Business Outcomes:
- Welch connected the success of Six Sigma to tangible business outcomes, underlining the direct impact of quality initiatives on a company’s bottom line.
4. Leadership Commitment to Process Improvement:
- His personal commitment to Six Sigma’s implementation highlighted the role of leadership in driving and sustaining process improvement initiatives.
5. Training and Empowering Employees:
- The initiative involved extensive training of GE employees in Six Sigma methodologies, illustrating the importance of equipping teams with the skills to drive quality improvements.
Concluding Thoughts
Jack Welch’s drive to implement the Six Sigma quality initiative at GE was a game-changing decision that extended beyond process improvement; it was about instilling a mindset of excellence and precision.
This initiative is a compelling case study of how a commitment to quality and continuous improvement can transform an organization, enhancing both operational efficiency and customer satisfaction. Welch’s leadership in this endeavor offers profound lessons on the power of quality initiatives in shaping successful, competitive businesses.
Your Reflection
Reflect on the Six Sigma initiative at GE and consider:
- How can you integrate a focus on quality and continuous improvement in your organization or team?
- What strategies can you employ to link quality initiatives to measurable business outcomes?
- How can you ensure a commitment to quality is embedded within your organization’s culture?
- What steps can you take to train and empower your team to contribute to continuous improvement processes?